Les métaux stratégiques compatibles avec une industrie responsable ? Leur utilisation croissante dans les applications digitales et les énergies renouvelables risque d’entraîner des tensions économiques et géopolitiques. La dépendance commerciale vis-à-vis de la Chine et de pays en guerre préoccupe l’industrie européenne. La conférence Métal Gagnant, organisée par l’industrie des métaux le 3 décembre, a placé la transition numérique et écologique au coeur des débats. La prise de conscience des pouvoirs publics et des industriels, exploitants miniers et transformateurs, ouvre la porte aux innovations technologiques et au recyclage.
Après la thématique sur le Grand Paris abordée l’an dernier, l’Alliance des minerais, minéraux et métaux (A3M) a choisi la transition numérique et écologique pour organiser sa 2e édition Métal Gagnant, sous la présidence de Catherine Tissot-Colle. Invité de la conférence, Cédric Villani, député LREM et mathématicien, lauréat de la médaille Fields, n’a pas manqué de souligner les paradoxes de l’intelligence artificielle, dans un rapport remis au gouvernement au printemps dernier : « ce secteur d’activité contribue à l’économie des ressources grâce au stockage de données et à la dématérialisation, mais dans le même temps, représente l’une des activités humaines les plus énergivores et consommatrices de matières premières tels que certains métaux critiques. Nous sommes face à une équation difficile sur le plan environnemental ».
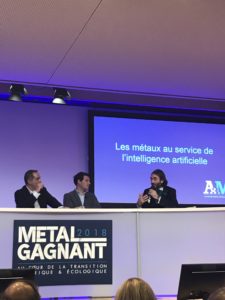
Si le numérique contribue fortement à la production de gaz à effet de serre, il a également besoin d’importantes quantités de métaux pour se développer. En Europe, la dépendance d’approvisionnement vis-à-vis des matières premières critiques semble inexorable au fur et à mesure du basculement vers une transition énergétique. Et cela ne fait que déplacer le problème, de la consommation de matières fossiles aux matières minérales et métalliques, dont les réserves souterraines sont encore aujourd’hui très mal connues. « Nous devons dans cette optique travailler sur un nouveau modèle économique qui concilie global et local » ajoute Cédric Villani. Pour Victoire de Margerie, vice-présidente du World Materials Forum, le doublement de la consommation des métaux à terme, pose le problème de la criticité. Six critères pour définir cette criticité ont été établis par le World Materials Forum : l’état des réserves, la demande industrielle, l’offre mondiale, les filières de recyclage, le contexte géopolitique des lieux d’extraction, les secteurs industriels les plus exposés (aéronautique et défense par exemple).
Un label responsable européen
« Malgré ces risques potentiels, nous observons en parallèle une multitude d’actions et de travaux de R&D menés au niveau international. L’exemple de BMW travaillant sur un moteur électrique sans utiliser de terre rare ou bien l’annonce de l’institut allemand Frauenhofer de fabriquer des aimants permanents sans terre rare sont des points positifs pour l’avenir » se réjouit Victoire de Margerie.
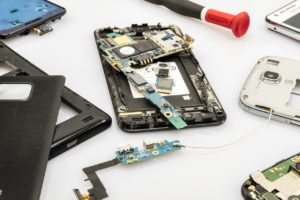
Depuis 2008, la commission européenne réactualise une liste de métaux stratégiques pour l’industrie, qui s’élève désormais à 27. Pourtant, Bruxelles reste timoré face à la nature de certains produits entrant sur son marché. Présidente du groupe Eramet, Christel Bories dénonce des pratiques peu respectueuses de l’environnement qui pourraient être sanctionnées par l’Europe mais qui ne le sont pas actuellement. « Des exploitants chinois de nickel en Indonésie n’hésitent pas à rejeter leurs déchets industriels directement dans l’océan. Ne pourrait-on pas exiger de l’Europe un label responsable sur l’importation de produits finis comme les batteries, dont on connaît l’origine de fabrication ? » ajoute-t-elle. L’absence de règles du jeu, équitables pour tous sur le marché des métaux, crée de plus en plus de tensions entre industriels et entre pays. D’où la nécessité de mettre en œuvre d’importants moyens pour promouvoir l’économie circulaire dans ce secteur. Le recyclage et la prévention en font partie. Plusieurs travaux de R&D dans le monde sont en cours pour remplacer certains métaux par d’autres moins stratégiques. Le cobalt utilisé dans les batteries pourrait être ainsi remplacé par du nickel-manganèse. Au Japon, l’aluminium pourrait également se substituer au cuivre dans le câblage électrique. Cela favoriserait des économies financières et une division de la production de câbles par deux.
Recycler sans perdre la qualité
Les perspectives des métaux critiques ne peuvent être évoquées sans aborder leur filière de recyclage. Alors que pour de nombreux métaux comme l’acier, l’inox ou l’aluminium, le recyclage est ancré depuis des décennies dans une industrie viable, celui des métaux stratégiques est plus problématique. Les quantités utilisées dans l’industrie (smartphones ou connectique par exemple) sont parfois si ténues que les procédés de traitement reviennent plus chers que la valeur propre de la matière. Autre difficulté, celle de la qualité de la matière recyclée. Un alliage d’aluminium issu du recyclage automobile ou de l’aéronautique ne pourra jamais retourner dans son application initiale. Pourtant, quelques initiatives tendent à enrayer cette fatalité. Eric Nottez, président de la Snam, est bien placé pour le savoir. Reconnue pour son expertise dans le recyclage des batteries électriques, des piles et des accumulateurs, cette société basée en Isère, parvient à recycler plus de 50 % du gisement, en partenariat avec le CEA de Grenoble et plusieurs marques automobiles dans le cadre d’accords de filière depuis 2012 : « cela nous a permis de réaliser de la R&D à coût partagé avec des résultats à la clef, et encore de nombreux projets, tel que Phénix, lancé il y a un an ».
Il s’agit ni plus ni moins de monter d’ici à six ans, une usine de fabrication de batteries neuves issues à 80 % de composants recyclés. Ces batteries neuves, constituées de composants récupérés (cellules, circuits imprimés, micro processeurs, câblages, boîtiers…), seront destinées à des applications stationnaires (modules-packs, armoires modulaires ou containers), principalement pour du stockage et de la conversion d’énergie. La demande en énergie est croissante et les problématiques de stockage d’énergie vont se développer. Le développement industriel se fera en six étapes avec l’ambition de recruter 645 personnes pour un investissement global de 25 millions d’euros.
La Chine produit aujourd’hui 40 % de l’énergie verte du monde. Le véhicule électrique devrait conquérir 6 % du marché automobile en 2022. « Pour donner à ce véhicule électrique de véritables vertus écologiques, nous devons nous pencher non seulement sur l’origine des composants et sur leur recyclage mais aussi sur la consommation électrique. Produire de l’électricité à partir de combustible fossile est un non sens. Il faut développer en parallèle suffisamment d’énergie décarbonnée pour pérenniser cette industrie » insiste Marc Mortureux, directeur général de la plateforme automobile (PFA). « Au-delà des enjeux du recyclage, l’industrie sidérurgique et métallique doit faire des efforts dans son outil de production pour réduire ses émissions de CO2 et recycler ses déchets. Des innovations technologiques sont indispensables dans les hauts-fourneaux par exemple », selon Philippe Darmayan, président de l’UIMM. Quelques projets témoignent d’ores et déjà d’avancées prometteuses.
Hymag’In, start-up de la magnétite
La toute jeune start-up grenobloise, Hymag’In, a développé un procédé pour valoriser les déchets et coproduits ferreux. Elle est accompagnée au sein de l’incubateur SATT Linksium de Grenoble et soutenue par le pôle de compétitivité Axelera. Il y a cinq ans, Camille Crouzet chercheur à l’université de Grenoble, prépare un doctorat sur la valorisation des déchets ferreux. Sa thèse soutenue en 2016, porte sur deux axes de recherche, l’extraction d’oxydes de fer, la magnétite, et la production d’hydrogène à partir de ces déchets. Ces produits sont présents dans de nombreux secteurs industriels, en particulier la sidérurgie et la métallurgie.

En poursuivant ses recherches sur l’utilisation industrielle de cette magnétite, Camille Crouzet décide de créer la start-up Hymag’In avec deux autres collaborateurs, Philippe Le Bouteiller, directeur développement et Céline Bonnaud, directrice recherche & innovation. Produite dans des tailles inférieures au micromètre, la magnétite revêt des propriétés physico-chimiques spécifiques (adsorption, oxydoréduction, magnétisme) qui en font un matériau très convoité. Elle est en particulier reconnue pour sa capacité à traiter des pollutions d’origine ménagère et industrielle comme l’arsenic, ou le chrome hexavalent ainsi que les micro-polluants organiques (résidus de médicaments, pesticides, hydrocarbures). Cette matière issue du recyclage pourrait ainsi devenir un substitut, en adsorption, ou un complément en oxydoréduction, du charbon actif. Autre atout, sa faculté d’aimantation, qui lui permet une séparation facile du milieu dans lequel elle est plongée. La technologie, brevetée, est centrée sur une réaction d’oxydation hydrothermale (maintien d’eau liquide à 200 °C) réalisée dans un autoclave. Celle-ci convertit alors la totalité du fer contenu dans le déchet en magnétite. Les déchets ciblés sont les poussières métalliques produites en très grand volume par la sidérurgie et pour lesquelles il n’existe pas aujourd’hui de solution de valorisation économiquement viable.
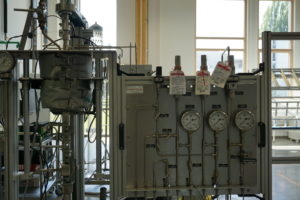
Un million de tonnes de coproduits ferreux sous forme de fines seraient ainsi générées chaque année en France, dont une grande majorité issue de la sidérurgie. Les enjeux économiques et environnementaux sont de taille. « Si la matière première à valoriser ne manque pas, il nous faut néanmoins trouver un équilibre économique entre l’offre et la demande. Notre modèle repose non pas sur le coût de reprise de ces déchets, mais bien sur la valeur ajoutée que l’on apporte à nos clients industriels en aval » souligne Céline Bonnaud. En recherche de partenaires industriels, Hymag’In est passé du laboratoire au pilote de démonstration. « Nous pouvons grâce à notre procédé, produire 250 kg de magnétite par an. Le changement d’échelle sera progressif avec une montée en puissance à 200 tonnes par an d’ici fin 2019-2020, explique Céline Bonnaud. Et l’objectif d’ouvrir le marché et de passer à une production de 10 000 t/an de magnétite en 2023 ».
Crédit : Hymag’In, CM
A lire aussi :