En France, l’entité ArcelorMittal Atlantique et Lorraine est implantée sur sept sites. Au coeur du dispositif, le complexe sidérurgique ArcelorMittal Dunkerque réalise 70 coulées par jour, soit l’équivalent de deux tours Eiffel et demi. Proche de la zone portuaire et d’un carrefour commercial stratégique, l’aciérie de Dunkerque engage près de dix millions d’euros par an pour réduire son empreinte environnementale. Ses investissements ciblent notamment depuis plusieurs années, le recyclage des ferrailles, la valorisation des laitiers et l’exploitation de la chaleur fatale.
Avec ses sept millions de tonnes d’acier produites en 2017, sous forme de brames et de bobines et ses quelque 3300 employés, ArcelorMittal Dunkerque est au centre d’une industrie dynamique régionale, qui a su rebondir par l’innovation et la prise en compte des préoccupations environnementales. Le site est l’un des seuls du groupe sidérurgique à consommer plus de 15 % de matières recyclées sur l’ensemble de ses approvisionnements, avec une croissance de un point chaque année.
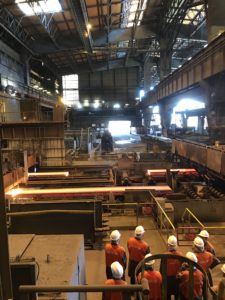
Selon Dominique Pair, directeur du site dunkerquois, cette évolution est possible de façon graduelle en recyclant une majorité de ferrailles produites en interne (à hauteur de 60 %). Le reste est constitué par les emballages en acier issus de la collecte sélective de la moitié Nord de la France, les gisements diffus provenant des chantiers de ferrailles, mais aussi les mâchefers ferreux générés par les unités de valorisation énergétique (UVE). « Pour des raisons techniques et de qualité, la part de matière recyclée utilisée à Dunkerque ne devrait toutefois pas dépasser à terme les 20 % » souligne Dominique Pair. Ici, la température des fours monte à plus de 1000°C. La transformation de l’acier est réalisée en coulée continue, depuis le fonctionnement des trois convertisseurs jusqu’à la production des brames, avant laminage. L’usine peut créer quelques 200 nuances d’acier différentes selon les applications industrielles. Pour y parvenir, la préparation de la matière ressemble à une grande cuisine où l’oxygène, la fonte, les ferrailles et d’autres matières sont injectées selon la composition souhaitée. Ce savant dosage repose essentiellement sur un tri préalable des matières recyclées en fonction de leur composition et leur teneur en fer.
Deux tours Eiffel et demi par jour
La préservation des ressources et leur recyclage sont néanmoins pris en compte dès l’étape de production de fonte dans les trois haut-fourneaux de l’usine. D’une capacité de 6,8 millions de tonnes, les hauts-fourneaux dunkerquois n’intègrent que cinq kilos de ferrailles par tonne de métal produite, alors que les aciéries électriques consomment 100 % de ferrailles pour leur production comme celle d’ArcelorMittal Industeel du Creusot qui enfourne entre 50 000 et 70 000 t/an de ferrailles, sans compter les chutes internes. C’est en effet lors de l’étape suivante, à l’aciérie, que la fonte est transformée en acier et que les ferrailles sont ajoutées. Cela n’empêche pas une innovation constante en vue de valoriser un maximum de co-produits industriels à Dunkerque. A commencer par les gaz de cokerie, composés entre autres de soufre. ArcelorMittal a investi en 1998 et 2015, dans un procédé d’extraction dans les gaz, de soufre pur à 99 %. Celui-ci qui était alors un polluant, est ainsi aujourd’hui valorisé dans l’industrie de la peinture et de la cosmétique.
Recyclage du laitier et des boues
Grâce à Ecocem France, créée sous forme de joint-venture en 2007 avec le groupe irlandais Ecocem Materials, ArcelorMittal valorise également son laitier de haut-fourneau en substitut de roche naturelle. Une fois granulé, le laitier est moulu par Ecocem pour entrer dans la composition du ciment. Après le lancement en 2009 d’une première unité à Fos-sur-Mer, un nouveau site de production a démarré à Dunkerque il y a quelques jours. ArcelorMittal a investi 18,5 millions d’euros dans l’achat de deux granulateurs. Ecocem utilise également les gaz émis par les hauts-fourneaux pour sécher la matière. Selon les prévisions, une année de production de l’usine Ecocem de Dunkerque évitera l’émission de 492 000 tonnes de C02.
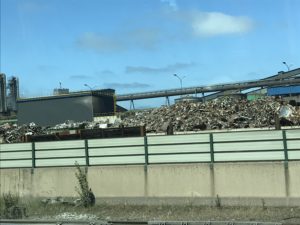
Autre projet, celui d’extraire et de valoriser les métaux contenus dans les boues sidérurgiques. Baptisé Ciroval, ce projet est réalisé en partenariat avec le groupe Paul Wurth spécialiste de l’ingénierie des haut-fourneaux sidérurgiques, et soutenu par le Pôle Team 2 dans le cadre de la promotion des équipementiers pour le recyclage. Ainsi, les poussières contenues dans les gaz de hauts-fourneaux sont douchées et récupérées sous forme de boues. Le procédé hydro-métallurgique proposé par Paul Wurth permettrait d’extraire puis de séparer le zinc et le plomb contenus dans ces boues. Ces métaux empêchent un recyclage en interne et sont mis en décharge. Aujourd’hui, le procédé est au point ; reste à valider sa faisabilité technique et économique. La construction d’une usine pilote grandeur nature sur le site de Dunkerque, pourrait être lancée d’ici à 2019, en vue de démarrer les premiers tests fin 2019. A la clef, la valorisation de 15 000 t/an de boues sèches sur ce site industriel.
La chaleur fatale au service du réseau urbain
La valorisation ne s’arrête pas là. A l’échelle du groupe, Dunkerque intègre les meilleurs procédés industriels en Europe pour récupérer et valoriser son énergie. L’exploitation de la chaleur de l’usine pour chauffer la ville de Dunkerque remonte à 1982. Mais des projets d’extension du réseau sont dans les tuyaux. Le principe est simple : sur les deux chaînes d’agglomération de l’usine, où le mélange de minerais fins est porté à haute température (1000°C), ArcelorMittal récupère cette chaleur grâce à un échangeur. L’air à 250°C chauffe l’eau, qui est ensuite envoyée au réseau municipal. Sur le réseau dunkerquois, cette chaleur véhiculée par de l’eau à 110°C permet de chauffer 6000 logements, l’hôpital, des écoles et la piscine. Cette opération évite l’émission de 450 000 tonnes de CO2. « La connexion avec le réseau de Grande-Synthe, proche du site sidérurgique est à l’étude pour un démarrage en 2020 » indique Dominique Pair. L’idée serait d’utiliser la chaleur produite par une chaudière utilisant les gaz sidérurgiques. A Dunkerque, 4,7 milliards de m³ de gaz sont traités chaque année pour produire l’équivalent de 200 MW, soit la consommation d’une ville de 200 000 habitants. Bien plus que les besoins de l’usine. Le surplus est revendu au réseau et à terme, moins de 5 % du gaz émis sur le site de Dunkerque sera brûlé.
En chiffres :
- Dans le monde, ArcelorMittal emploie 197 000 personnes avec des implantations dans 16 pays, qui fournissent l’industrie automobile, la construction, l’électroménager et l’emballage. Sa production d’acier en Europe pour l’emballage s’élève à 1,4 million de tonnes, pour une consommation européenne d’emballages acier de 4,6 millions de tonnes. ArcelorMittal fait partie des dix premiers producteurs qui fournissent 68 % de la consommation mondiale. Parmi les actions menées sur l’environnement, l’allègement en poids des emballages a atteint 30 % entre 1986 et 2016, à cahier des charges identique. L’objectif est de poursuivre cet allègement au cours des prochaines décennies, en visant une réduction supplémentaire de 20 %.
- Le recyclage des emballages en acier en Europe a atteint un nouveau record de 79,5 %, et devrait parvenir facilement à l’objectif de 80 % d’ici 2020, selon les chiffres de l’association des producteurs européens de l’acier pour emballages, APEAL. Le secteur enregistre une croissance constante du recyclage depuis 2016. Cela signifie que pour 10 emballages en acier mis sur le marché européen, près de 8 sont collectés et recyclés. En France, le taux se trouve au-dessus de la moyenne européenne, à 83 % (chiffre 2016 Ademe). ArcelorMittal a recyclé en 2017 sur ses deux sites de Dunkerque et de Fos-sur-Mer, 42 000 tonnes de déchets d’acier issus de la collecte sélective, soit une croissance de 8 % par rapport à 2016.
Crédit : CM
A lire aussi :